چگونه کمپرسور اسکرو مناسب برای دستگاه شیشه سازی خود را انتخاب کنیم؟
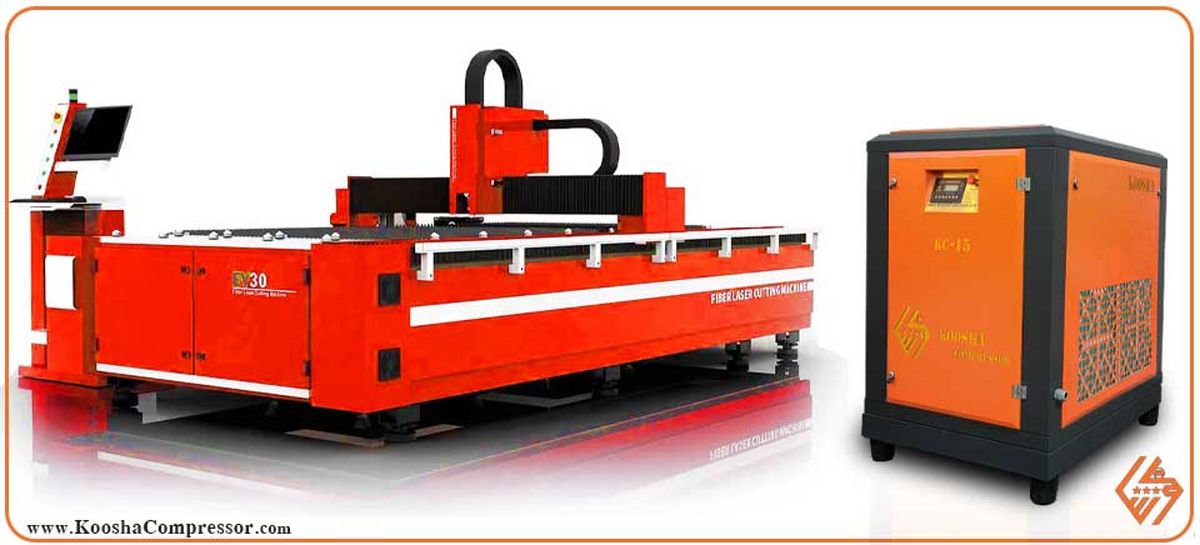
در صنعت شیشه سازی، کیفیت و کارایی تجهیزات نقش بسزایی در موفقیت تولید دارد. یکی از مهمترین قطعات در این صنعت، کمپرسور اسکرو است که به عنوان قلب تپنده خط تولید شناخته میشود. انتخاب کمپرسور اسکرو مناسب میتواند تأثیر قابل توجهی بر راندمان تولید، کیفیت محصول نهایی و هزینههای عملیاتی داشته باشد. در این مقاله، راهنمای جامعی برای انتخاب بهترین کمپرسور اسکرو برای دستگاههای شیشه سازی ارائه میدهیم.
اهمیت کمپرسور اسکرو در صنعت شیشه سازی
فرآیند شیشه سازی نیازمند هوای فشرده با کیفیت بالا و فشار ثابت است. کمپرسورهای اسکرو به دلیل قابلیت تولید هوای فشرده با فشار یکنواخت، بدون ضربان و با کیفیت بالا، گزینه ایدهآلی برای صنعت شیشه سازی محسوب میشوند. این کمپرسورها برخلاف انواع پیستونی، جریان هوای پیوسته و بدون نوسان ارائه میدهند که برای فرآیندهای حساس شیشه سازی بسیار مهم است.
فاکتورهای کلیدی در انتخاب کمپرسور اسکرو مناسب
۱. ظرفیت و دبی هوای مورد نیاز
اولین و مهمترین فاکتور در انتخاب کمپرسور اسکرو، تعیین میزان هوای فشرده مورد نیاز خط تولید است. این مقدار بر حسب CFM (فوت مکعب در دقیقه) یا لیتر بر ثانیه اندازهگیری میشود. برای محاسبه دقیق این مقدار، باید:
- تمام تجهیزات مصرفکننده هوای فشرده در خط تولید را شناسایی کنید
- میزان مصرف هر دستگاه را مشخص نمایید
- ضریب همزمانی کارکرد تجهیزات را در نظر بگیرید
- حداقل ۲۰٪ ظرفیت اضافی برای توسعههای آینده لحاظ کنید
برای یک خط تولید شیشه متوسط، معمولاً کمپرسورهای با ظرفیت ۱۰۰ تا ۵۰۰ CFM مناسب هستند، اما این مقدار با توجه به ابعاد خط تولید میتواند متغیر باشد.
۲. فشار کاری مورد نیاز
فشار کاری در صنعت شیشه سازی معمولاً بین ۷ تا ۱۰ بار است. این فشار باید متناسب با نیاز دستگاههای شیشه سازی باشد. انتخاب کمپرسور با فشار بیش از حد نیاز، منجر به اتلاف انرژی و هزینههای اضافی میشود. به یاد داشته باشید:
- حداکثر فشار مورد نیاز حساسترین دستگاه در خط تولید را مشخص کنید
- افت فشار در مسیر لولهکشی (معمولاً ۰.۵ تا ۱ بار) را در نظر بگیرید
- کمپرسوری انتخاب کنید که فشار خروجی آن حداقل ۱ بار بیشتر از فشار مورد نیاز باشد
۳. کیفیت هوای خروجی
در فرآیند شیشه سازی، کیفیت هوای فشرده از اهمیت بالایی برخوردار است. وجود ذرات معلق، روغن یا رطوبت در هوای فشرده میتواند منجر به عیوب متعددی در محصول نهایی شود. بنابراین:
- سیستم تصفیه هوای مناسب شامل فیلترهای ورودی، فیلترهای روغن و خشککن را در نظر بگیرید
- برای فرآیندهای حساس، کمپرسورهای بدون روغن (Oil-Free) یا تزریق آب (Water-Injected) را مد نظر قرار دهید
- سیستم جداکننده آب و روغن کارآمد برای کاهش آلودگیهای زیستمحیطی انتخاب کنید
۴. راندمان انرژی
هزینههای انرژی معمولاً حدود ۷۰٪ از هزینههای طول عمر یک کمپرسور را تشکیل میدهند. بنابراین، انتخاب کمپرسور با راندمان بالا میتواند صرفهجویی قابل توجهی در هزینهها داشته باشد:
- کمپرسورهای مجهز به اینورتر (VSD یا Variable Speed Drive) را انتخاب کنید که مصرف انرژی را متناسب با نیاز تنظیم میکنند
- به شاخص Specific Power یا kW/CFM توجه کنید (هرچه کمتر باشد، راندمان بالاتر است)
- سیستمهای بازیافت حرارت را برای استفاده از گرمای تولیدی کمپرسور در سایر فرآیندها در نظر بگیرید
۵. قابلیت اطمینان و دوام
در صنعت شیشه سازی، توقف ناگهانی خط تولید به دلیل خرابی کمپرسور میتواند هزینههای هنگفتی به همراه داشته باشد. بنابراین:
- کمپرسورهای با برند معتبر و سابقه عملکرد مطلوب را انتخاب کنید
- به گارانتی، خدمات پس از فروش و در دسترس بودن قطعات یدکی توجه داشته باشید
- سیستم کنترل و مانیتورینگ پیشرفته برای تشخیص زودهنگام مشکلات احتمالی را مد نظر قرار دهید
- سیستمهای دوگانه یا پشتیبان را برای جلوگیری از توقف کامل خط تولید در نظر بگیرید.
انواع کمپرسورهای اسکرو مناسب برای صنعت شیشه سازی
کمپرسورهای اسکرو روغنی (Oil-Injected)
این نوع کمپرسورها رایجترین نوع در صنعت شیشه سازی هستند. روغن در این کمپرسورها برای روانکاری، آببندی و خنککاری استفاده میشود. مزایای آنها عبارتند از:
- قیمت مناسبتر نسبت به انواع بدون روغن
- راندمان بالاتر و مصرف انرژی کمتر
- عمر طولانیتر قطعات به دلیل روانکاری مناسب
البته باید توجه داشت که نیاز به سیستمهای تصفیه پیشرفته برای جداسازی روغن از هوای خروجی دارند.
کمپرسورهای اسکرو بدون روغن (Oil-Free)
برای کاربردهایی که نیاز به هوای کاملاً عاری از روغن است، این نوع کمپرسورها ایدهآل هستند:
- حذف خطر آلودگی محصول با روغن
- کاهش هزینههای تصفیه و فیلتراسیون
- کاهش هزینههای زیستمحیطی مرتبط با دفع روغن
معایب آنها شامل قیمت بالاتر، راندمان کمتر و هزینه نگهداری بیشتر است.
کمپرسورهای اسکرو تزریق آب (Water-Injected)
این کمپرسورها جایگزین مناسبی برای انواع بدون روغن هستند که از آب برای روانکاری و خنککاری استفاده میکنند:
- تولید هوای فشرده عاری از روغن
- دمای خروجی پایینتر
- قیمت مناسبتر نسبت به انواع بدون روغن
البته نیاز به تصفیه آب و سیستم تصفیه پساب از معایب آنها محسوب میشود.
محاسبه هزینههای کل مالکیت (TCO)
برای انتخاب اقتصادیترین گزینه، باید هزینههای کل مالکیت را در نظر بگیرید:
هزینههای اولیه
- قیمت خرید کمپرسور
- هزینههای نصب و راهاندازی
- تجهیزات جانبی مانند فیلترها، خشککن و مخزن ذخیره
هزینههای عملیاتی
- مصرف انرژی (معمولاً ۷۰٪ از کل هزینهها)
- هزینههای نگهداری و تعمیرات
- تعویض روغن و فیلترها
- قطعات یدکی و سرویسهای دورهای
برای محاسبه دقیق، هزینههای ۵ تا ۱۰ سال آینده را با در نظر گرفتن تورم و افزایش قیمت انرژی محاسبه کنید.
تکنولوژیهای نوین در کمپرسورهای اسکرو
سیستمهای کنترل هوشمند
کمپرسورهای مدرن مجهز به سیستمهای کنترلی پیشرفته هستند که قابلیتهایی مانند:
- تنظیم خودکار فشار و دبی متناسب با نیاز
- مانیتورینگ آنلاین و هشدار زودهنگام مشکلات
- قابلیت برنامهریزی زمانی برای کارکرد در ساعات غیر پیک مصرف برق
- امکان اتصال به سیستم BMS ساختمان و کنترل از راه دور
سیستم مدیریت چند کمپرسور
برای مجموعههایی با چندین کمپرسور، استفاده از سیستمهای مدیریت مرکزی میتواند راندمان را تا ۳۰٪ افزایش دهد:
- توزیع بار بین کمپرسورها به صورت بهینه
- کاهش زمان کارکرد در حالت بیباری (Unload)
- افزایش طول عمر کمپرسورها با توزیع متوازن کارکرد
ملاحظات نصب و راهاندازی
موقعیت مکانی مناسب
محل نصب کمپرسور تأثیر زیادی بر عملکرد و طول عمر آن دارد:
- فضای کافی برای تهویه و دسترسی جهت تعمیرات (حداقل ۱ متر از هر طرف)
- دمای محیط مناسب (بین ۵ تا ۴۰ درجه سانتیگراد)
- سطح صاف و محکم با فونداسیون مناسب برای کاهش ارتعاشات
- نزدیکی به محل مصرف برای کاهش افت فشار در مسیر لولهکشی
سیستم لولهکشی
طراحی صحیح سیستم لولهکشی میتواند افت فشار را به حداقل برساند:
- استفاده از لولهها با قطر مناسب (معمولاً بزرگتر از خروجی کمپرسور)
- طراحی سیستم به صورت حلقهای برای توزیع یکنواخت فشار
- استفاده از مواد مقاوم به خوردگی مانند آلومینیوم یا استنلس استیل
- نصب شیرآلات مناسب برای ایزوله کردن بخشهای مختلف سیستم در زمان تعمیرات
برنامه نگهداری و سرویس دورهای
برنامه نگهداری منظم برای اطمینان از عملکرد بهینه کمپرسور ضروری است:
سرویسهای روزانه و هفتگی
- بررسی سطح روغن و فشار کاری
- تخلیه آب از سپراتورها و فیلترها
- بررسی نشتیهای احتمالی
سرویسهای ماهانه و فصلی
- تعویض فیلترهای هوا
- بررسی عملکرد سیستم خنککننده
- کنترل سیستم کشش تسمه (در صورت وجود)
سرویسهای سالانه
- تعویض روغن و فیلتر روغن
- بررسی یاتاقانها و قطعات متحرک
- کالیبراسیون سنسورها و سیستمهای کنترلی
- آنالیز ارتعاشات برای تشخیص مشکلات احتمالی
دیدگاه تان را بنویسید